Industries We Serve
Optimize your operations and accelerate your journey to net zero
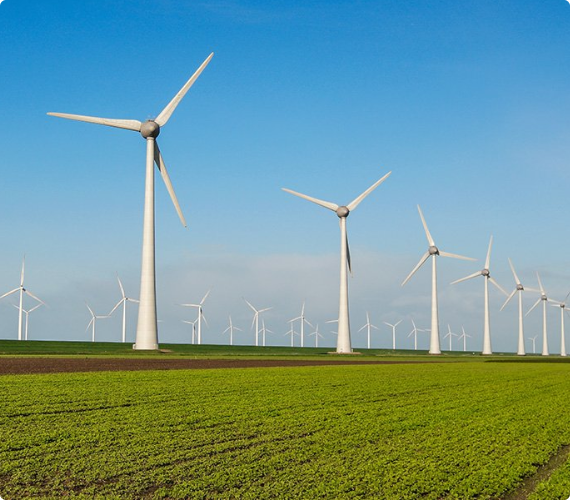
Renewable
Lower Downtime and Accelerate Learning
New Energies require new ways to manage risks for lowering LCOE. For wind, O&M costs around 30% of life cycle costs of which, 90% contribute to unplanned downtime. Lack of data results in wasteful design and reactive operations thereby increasing overall cost of operations.
Lifecycle condition data on key structures (Blades, tower, foundation) provide actionable insights for early anomaly detection and predictive maintenance. Continuous learning enable accurate training of analytical models for lowering O&M costs and improvement in future design.
Rapid Turnaround and Lower Maintenance Costs
Refineries of the future require smarter ways to manage risks. Manpower intensive inspections especially in hard to reach confined spaces results in higher costs and poor data quality. Ageing facilities and severe environment pose increasing risks for unplanned downtime and leaks.
Lifecycle data on key structures (coke drum, pressure vessels, storage tanks, piping system, flare booms) provide actionable insights for early anomaly detection and predictive maintenance. Automated inspections enable rapid turnaround and lower maintenance costs.
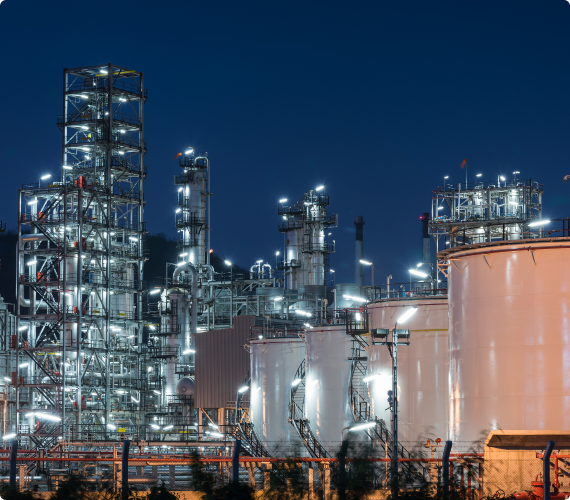
Refining and Petrochemical
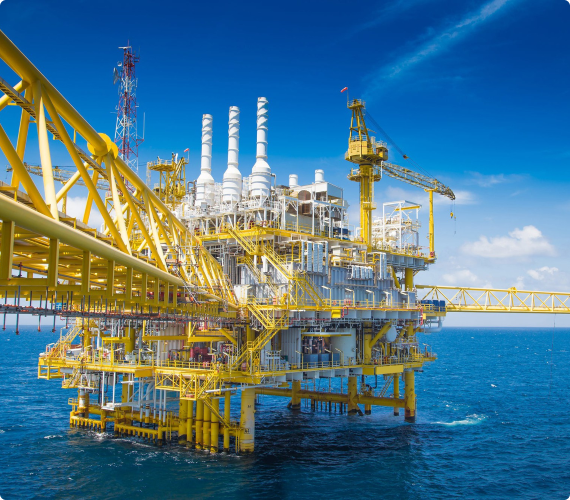
Pipeline and Offshore/Onshore Facilities
Optimize Maintenance and Manage Compliance
Fields of the future require quality data to optimize operations. Remote pipelines and energy facilities are operated with limited dataset due to personnel access restrictions access to power for vast infrastructure monitoring. Re-purposing of existing infrastructure for new energy generation and storage (e.g. Hydrogen) lead to new safety concerns (cracking, erosion) demanding rigorous inspection for compliant operations.
Lifecycle data on key structure (piping, hull structure, process equipment) provide actionable insights for optimized maintenance and compliance operations. Distribute sensor network and wireless connectivity provides enhanced visibility for safe operations and life extension.
Enhanced Uptime and Accurate Condition Tracking
Smart mining equipment require smart way to manage risk in harsh operating environment. Schedule inspections results in higher costs and limited condition data. Limited connectivity in remote locations results in costly breakdown.
Lifecycle data on critical equipment (cranes, dozers, loaders) provide actional data for early anomaly detection and predictive maintenance. Connected operation enable enhanced uptime and accurate condition tracking of critical equipment.
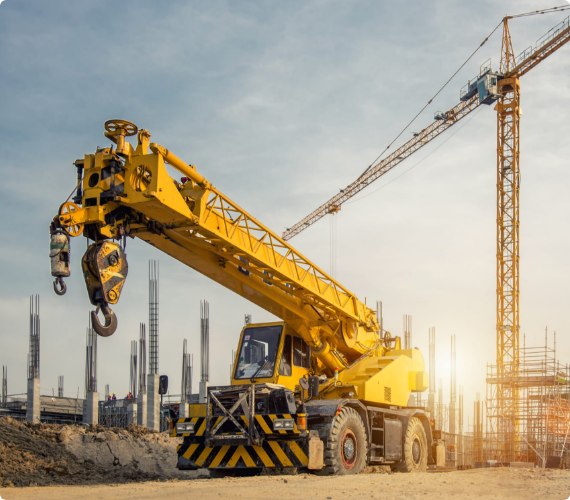
Mining
Benefits
IoT platform delivers operations and condition data at a fraction of costs than existing tools.
Enhance visibility of operations and maintenance with data driven predictive planning.
Condition tracking allow re-use or continued usage of equipment and critical infrastructure.
Minimize number of on-site personnel from hazardous areas and enable remote monitoring.
Improve sustainability and reduce environmental impact from battery change-outs and personnel movement.
Key data to simplify regulatory compliance and avoid violations.
Continuous tracking allow early warning for safety critical events.
Early warning of threats and optimized inspection resulting for predictive operations.